Like every other type of welding in Australia, basic skills and understanding are vital for successful electrofusion. To make your job easier, we have compiled some electrofusion installation tips that our customers have found to be very beneficial and have listed them below.
Alignment
To ensure successful electrofusion welds are performed, poly pipe must be inserted 'straight' into the socket, i.e., the pipe must be aligned with the socket. The below image shows a cut-through section of an electrofusion joint that failed
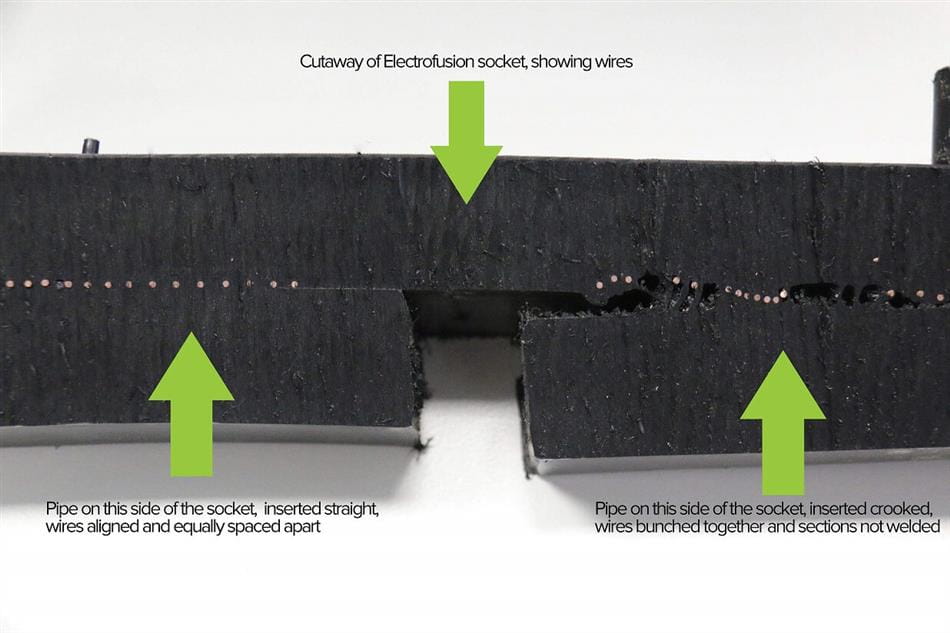
to retain pressure. Upon cutting through the socket, it was immediately apparent that the pipe on one side of the socket was inserted without being aligned. As the joint was being performed, the plastic melted, the wires in the electrofusion socket flowed with the molten plastic towards the opening, causing them to bunch together, resulting in a joint that was unsuccessful. This can be avoided by ensuring that pipe is inserted parallel with the socket and that there is no angular deflection.
Ambient temperature
Avoid fusing poly pipe in ambient temperatures that are below 5 Degrees Celsius. Electrofusion can be performed below this temperature, however it is difficult to ensure fittings are moisture free below this temperature and hence there’s a higher chance of moisture contamination. Moisture that is present during the fusion cycle heats up and eventually turning to steam, creates pockets of air in the joint interface, that will eventually allow water to track through and create a leak.
Weld straight after scraping
Poly pipe must be welded within 30 minutes of scraping, as UV / light quickly
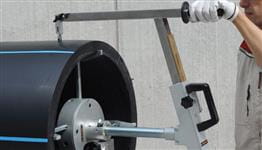
re-oxidises pipe surface, causing external surface to require a re-scrape. Oxidised polyethylene will not successfully weld. If re-scraping is required, be careful to ensure that pipe or fittings outside diameter is within manufacturer specified clearances tolerances.
Welding Wipes
Use only approved 90% alcohol Electro-fusion welding wipes and allow surface to
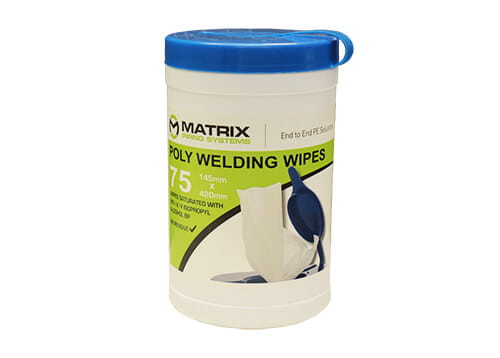
thoroughly dry before welding. Any moisture left between pipe and Electrofusion fittings during the weld cycle will turn to steam and cause partial or complete de-cohesion of pipe and fitting. Never use an alcohol wipe more than once. Reusing a wipe can re-introduce contaminants to the weld surfaces.
Never Re-use Welding Wipes
Never use an alcohol welding wipe more than once, discard every wipe after first use every time. Reusing a wipe can re-introduce contaminants to the weld surfaces. Further information is provided by these Electrofusion Guidelines by PIPA.
Keep Electrofusion Area Totally Dry
Keep welding area dry; if weather is damp, place tent and wind shield over weld area
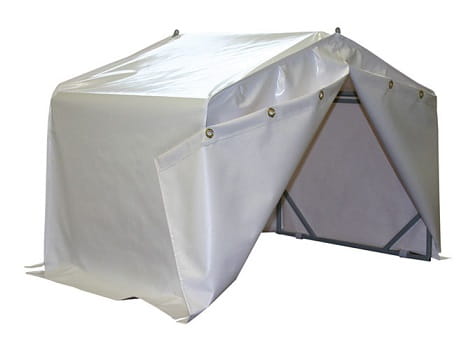
to keep moisture out of the electrofusion joint. The presence of any moisture during the weld cycle is very detrimental to electrofusion welding. Moisture is like a barrier to successful fusion of the two plastic surfaces that are being joined. As we all know, moisture, when it is heated up, eventually turns to steam, or a gas. The presence of a gas in the weld cycle causes voids to form, which will eventually cause joint failure, so keeping your welding area dry will prevent this from occurring. It is like a low price, once off guarantee against costly repairs.
Calibrate Your Welder 12 monthly
Electrofusion welder that are left longer than 12 months to be calibrated are likely to cause a joint failure due to potentially falling outside of correct parameters.
Do not touch weld surface
Never touch a prepped weld surface or the inside of a socket without cleaning it again. Finger prints can and will cause a weld joint failure. We recommend fittings are left in their bags right up until you are ready to weld.
Suitability Of fabricated fittings For EF
Unless the manufacturer advises that a fabricated fitting is suitable for electrofusion, do not assume that they are suitable. Sweeping bends and pulled tees can, by nature of their manufacturing process, become mis-shapen. We recommend that you ask the manufacturer of the fittings if they are suitable for electrofusion.
WELDING TRAINING
It pays to have all of your staff that perform electrofusion welding, trained by a PIPA recognised Registered Training Organisation. It is risky not to do so. This is especially important if your staff are welding on a pipeline that contains pressure above 10 Bar pressure. Poly welding courses that are performed on-site are even available.
INDICATOR PINS
As a general rule, if the indicator pins on both sides of the EF Socket do not pop up during the fusion cycle, you need to assume that the joint has not been successful and you should cut out the fitting and start again. There have been instances where the indicator pin on one side does not pipe for some reason, and the weld has successfully held for many years, however as a general rule, if the pins dont pop, chuck it out.
PIPE CLAMPS
Always use pipe clamps. Pipe clamps prevent the movement and misalignment of pipe during the welding process and thereby help installers control the process more thoroughly.
REVERTED PIPE ENDS
Most pipe ends revert (shrink) during the manufacturing process, and therefore it is essential that reverted ends are cut off. As a general rule, cut at least 50mm off every end of every pipe, to ensure the success of your electrofusion welds.
EF SADDLE INSTALLATION
Specific information on electrofusion saddle installation tips can be found by clicking on the link provided.
Please Note: The above tips are not designed to replace a proper, accredited training course, so we highly recommend that book your staff in for training, or if they are already trained, remember to book them in for a refresher course every 2 years. Further information on recommended electrofusion welding training can be found on Training.gov.au. The only guarantee that your staff will perform quality fusion joints, is that they are adequately trained for electrofusion, and that they follow industry best practice guidelines everytime.
Have an enquiry? Or is there something you'd like to see added here? Fill in the Contact form below.
Updated: 20th December 2016
Sales + Customer Service:
Head Office:
5 Richards Rd Swan Hill Victoria 3585
Melbourne Despatch:
2 Richards Circuit, Keilor Park Victoria 3042
(by appointment only)